Flotation is the most frequently used process in beneficiation equipment. It is a very important step in the entire production line. Flotation directly affects the quality of finished products. The importance of the flotation process can be imagined. Therefore, we must pay attention to every detail of flotation in production. In addition to these, we must also clearly know the important factors that affect the flotation process.
The poor flotation effect in production is a problem that many people will encounter. This article summarizes seven questions about the flotation machine effect, hoping to help your production.
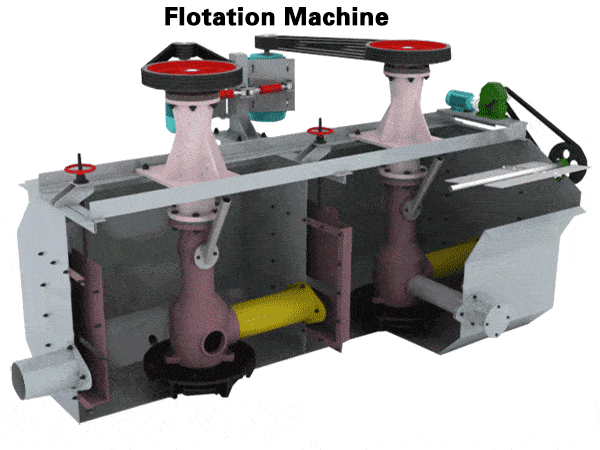
grinding particle size
During flotation, too coarse ore particles (greater than 0.1mm) and very fine ore particles (less than 0.006mm) do not float well, and the recovery rate is low.
1. In the flotation of coarse particles, due to the larger weight, the shedding force of the ore particles increases. The measures that need to be taken are: Use a sufficient amount of the most effective collector; Increase the aeration of the pulp to cause larger bubbles and increase the amount of microbubbles precipitated in the water; The stirring intensity of the pulp It should be appropriate; The pulp concentration should be appropriately increased; The scraper should be quick and stable when scraping the bubbles.
2. In the flotation of very fine particles (usually refers to the slime less than 5 ~ 10μm), the measures to be taken are:
- Selective flocculation and flotation; Use flocculant to selectively flocculate target mineral particles or gangue fine mud, and then use flotation to separate;
- Carrier flotation. The ore particles of general flotation size are used as the carrier to cover the fine particles of the target mineral on the carrier and float. The carrier can use the same kind of minerals or different kinds of minerals. For example, fine-grained gold can be flotated using pyrite as a carrier. Calcite is used as a carrier to float off the fine-grained iron and titanium impurities in kaolin.
- Agglomeration flotation, also known as emulsification flotation. After the fine-grained minerals are treated with collectors, under the action of neutral oil, they form oily foam with minerals. The collector and neutral oil can be formulated into an emulsion first and then added to the pulp. It is also possible to add neutral oil and collector separately to the pulp of high quality fraction (solid content up to 70%), stir vigorously, control the time, and then scrape out the upper layer of foam. This method has been used for fine-grained manganese ore, ilmenite and apatite.
water quality
The flotation process is mainly carried out in the water medium, so the water quality has a great influence on the flotation process and its indicators. Generally, flotation production water mainly includes soft water, hard water, salt water, saturated solution of salt and production backwater. Different production processes have different requirements for water quality. Generally, the water used for flotation should not contain a large amount of suspended solids and substances that react with flotation reagents or minerals. In addition, the dissolved oxygen content also has a significant impact on the flotation process indicators.
pharmaceutical preparation
Flotation reagents are divided into two types: solid and liquid. When adding in the flotation process, sometimes the solid agent is added directly, sometimes the stock solution is added, and sometimes the solid agent needs to be prepared into a certain concentration of liquid before adding. The form in which the medicament is added depends mainly on factors such as the solubility of the medicament, the action time, the dosage of the medicament and the operating conditions.
- Agents that are easily soluble in water (such as copper sulfate and xanthate) need to be prepared into a 5-20% solution;
- Agents that are slightly soluble in water (black medicine, oleic acid) can be formulated into low-concentration solutions or directly added to the grinder;
- Drugs that are insoluble in water can be dissolved in an organic solvent first, and then formulated into a low-concentration solution.
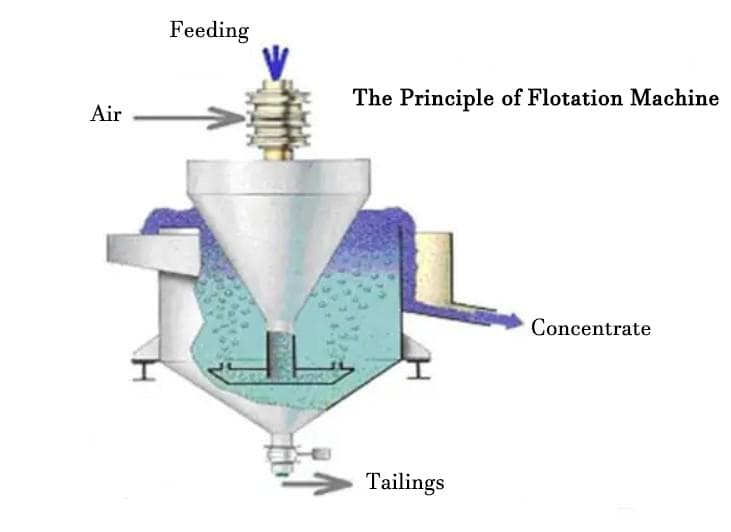
The effect of air on flotation
In addition to oxygen, nitrogen and inert gases, there are carbon dioxide gas and water vapor in the air. Air has a certain effect on mineral floatability:
- When the mineral is broken and exposed to the fresh surface, it will be hydrated when it encounters water, and it will be hydrophilic. However, when the gas is adsorbed to the mineral surface, it can weaken the hydration, resulting in the initial hydrophobicity of the surface.
- The use of gas and mineral surfaces is selective. Among them, oxygen has a greater impact on the surface of minerals.
- The role of oxygen is beneficial to the hydrophobicity of sulfide ore. However, if the action time is too long, the surface of the mineral will become hydrophilic. When the gas adsorption conditions are appropriate, it will cause the mineral surface to be hydrophobic, and it can be floated even without the addition of a flotation agent (eg dry pulverized coal).And galena can only float up after the initial action of oxygen.
The influence of slurry stirring
The stirring of the slurry can promote the suspension of the ore particles and the uniform dispersion in the tank. It can promote the good dispersion of the air and make it evenly distributed in the tank. It can promote the air to strengthen the dissolution in the high pressure area in the tank, and strengthen the precipitation in the low pressure area, so as to cause a large number of active microbubbles.
Strengthening aeration and agitation is beneficial to flotation, but it should not be excessive, because excessive aeration and agitation will produce the following disadvantages: Promote the merger of air bubbles; Reduce the quality of concentrates; Increase power consumption; Increase the wear of various parts of the flotation machine; The volume of the pulp in the tank is reduced (this is because the volume of the tank is increased by the part occupied by the bubbles); Excessive stirring may also cause the ore particles attached to the bubbles to fall off.
The optimum amount of aeration and agitation in production should be determined through experiments according to the type and structural characteristics of the flotation machine.
Too much slime in the grinding slurry
Common methods to prevent and reduce sludge are:
- Reduce and prevent the formation of ore slime: Multi-stage grinding process and stage beneficiation process can be used. It is necessary to correctly select grinding and classification equipment to improve the efficiency of the classifier;
- Add agents to eliminate the harmful effects of ore slime: water glass, soda, caustic soda, etc. are commonly used; it can reduce the flocculation cover effect of ore slime. In order to reduce the harmful effects of a large amount of adsorbents in the slime, it is possible to consider the use of staged dosing;
- Deslime the ground ore before flotation and discard it as tailings. If the content of useful components in the slime is high, the removed slime can also be treated by flotation alone or sent to water for smelting treatment.
Common desliming methods: ① Desliming by classifier; ② Desliming by hydrocyclone; ③ In special cases, a small amount of foaming agent can be added before flotation to remove easily floating sludge by flotation.
Influence of pulp concentration on flotation index
- Affect the recovery rate. When the pulp concentration is small, the recovery rate is low. When the pulp concentration increases, the recovery rate also increases, but the recovery rate exceeds the limit and decreases. The main reason is that the concentration is too high, which destroys the aeration conditions of the flotation machine.
- Affect the quality of concentrate. The general rule is that the concentrate quality is higher when flotation in a thinner pulp, and the concentrate quality is lower when flotation in a thicker pulp.
- Affect the consumption of medicine. When the pulp is thicker, the dosage per ton of ore is less, and when the concentration of the pulp is dilute, the dosage of medicine per ton of ore is increased.
- Affect the production capacity of the flotation machine. As pulp concentration increases, so does the capacity of the flotation machine in terms of throughput.
- Affecting water and electricity consumption. The thicker the pulp, the smaller the hydropower consumption per ton of ore processed.
- When flotation is affected. When the flotation pulp is thicker, the flotation time increases slightly.
In short, when the pulp concentration is thicker, it is beneficial to the flotation process. However, if it is too large, the pulp and air bubbles cannot flow freely, and the aeration effect will be deteriorated, thereby reducing the quality and recovery rate. Due to this difficulty, the flotation department of various ore should determine the appropriate slurry concentration according to the properties of the ore and related technical requirements.
In daily operations, in order to ensure that the flotation machine can maintain a continuous and stable flotation operation. The flotation machine operator should not only be familiar with the structure and working principle of the flotation machine, but also understand the flotation and particle size composition of the floating minerals, and the process factors that affect the flotation effect. In production, we must pay attention to every detail of the flotation process, and determine the process parameters according to the results of the scientific beneficiation test report, so as to obtain the ideal beneficiation plant benefit.